Page 1 of 1
Clone Wars style gauntlets
Posted: Wed Oct 03, 2012 8:34 pm
by gandalfbmg
A local workshop is doing a vacforming class at the end of this month, and I wanted to go to learn, but maybe do something with some costume use right off the bat too. so I'm going to start messing with making the bucks for Clone Wars style Jedi gauntlets...
I have a bunch of the pink insuation foam laying around so I took some measurements from my arm and started cutting:
Next is I know I need to figure out what to coat these in, to protect the foam from the heat and suction of the vac table, and to give me a surface I can smooth out and fill in the gaps (since I'm a terrible cutter and it's a hack job so far on the cutting. So hopefully I'll get some inspiration (or advice) on what routes I can go there...
Please be gentle, this is my first time ever trying anything like this...
Re: Clone Wars style gauntlets
Posted: Thu Oct 04, 2012 7:47 am
by Culvan
gandalfbmg wrote:Next is I know I need to figure out what to coat these in, to protect the foam from the heat and suction of the vac table, and to give me a surface I can smooth out and fill in the gaps
Looks like you are off to a good start. I've experimented with similar things with my vac table. The pink foam bonds with the HIPS sheets I'm using and it's terrible. I haven't gotten it to work, but at least I can tell you what hasn't worked.
In the picture below you will see pink foam insulation. I tried one plain as a control, it locked in real bad, the heat deformed it too so the pull was terrible. I tried spray paint. You'll notice that the red ones are pitted where the solvents in the spray paint ate the foam away. They also locked down and deformed under the vacuum. I tried a latex paint (the white one). It didn't pit, but it deformed and locked down. I tried sealing one with elmers glue and it was probably the most succesful. It released, but the heat and pressure deformed the foam.
I've heard (but never tried it) that resin, like smooth cast 300, can be used for strength and protection in Vacuumforming. Bondo is also strong enough, but will break down under the heat eventually. It also has solvents that will eat the foam when you apply it. I've had the most success with making a mold and casting it in Hydrocal. Unfortunately I was rushing to finish this so the mold was crap, but the the vacuuforming went well.
Let me know if you want to try out my rig for experimentation sometime. It's powered off a dryer's electrical hookup and designed to be transportable.
Andy
Re: Clone Wars style gauntlets
Posted: Thu Oct 04, 2012 8:08 am
by gandalfbmg
Yeah, I've read that you don't want to use the foam 'plain'. And from building the temple photo set I learned that spray paint and the foam don't mix, but latex paint is good. Glad to know that Bondo will do the same, I already have some on hand so was considering starting there for filling in some of the gaps, but I think I'll wait and see if I can't hunt something down like this Smooth Cast stuff...
And my hopes are that I can 'learn' on the rented table at Hammerspace, but once I've taken a class then I'll feel a little more comfortable working on the rigs of the people I actually know... I don't want to do that until I've had some education, I'm afraid otherwise I'd just know enough to be dangerous

Re: Clone Wars style gauntlets
Posted: Thu Oct 04, 2012 2:02 pm
by gandalfbmg
Got a tip to try this stuff... Anyone ever used it and have any feedback?
http://hotwirefoamfactory.com/-025-Foam-Coat-3lbs.html
Re: Clone Wars style gauntlets
Posted: Thu Oct 04, 2012 7:37 pm
by Culvan
I've never used it, but it seems similar to a few other ideas I've had. Spackle should be fairly heat resistant. Tile grout is heat resistant and doesn't shrink. The downside is that if you put on enough to shield the foam underneath from the heat then you are going to have to remake all your details.
I've suspected that it would be better to use potter's clay to make the original. It can be sculpted with simple tools. Smoothed with water. Hardened by heat. The bad thing is that it won't last through a lot of cycles, but if you get one good pull you can backfill it with hydrocal to make a new buck.
Andy
Re: Clone Wars style gauntlets
Posted: Thu Oct 04, 2012 7:56 pm
by gandalfbmg
I don't have detail in the foam, I made it a little small so the foam shape could be rough and fill in imperfections and worry about finishing on the cover material. And the only detail will be the seam from the elbow and arm, and that's not this piece.
Re: Clone Wars style gauntlets
Posted: Wed Oct 10, 2012 8:52 am
by gandalfbmg
Well, I've finally gotten the 'top' half roughed out. I ordered some of the Foam Coat stuff too and it's on the way. Knowing that I was a little less careful this time so the cuts are a lot less smooth. I'll make it up on the filling/sanding. I'm not quite skilled with the hot foam cutter yet, and it shows...
I do think my plan will be to try and get a good pull from these and use to make a more permanent bucks from, out of a more resilient material.
Re: Clone Wars style gauntlets
Posted: Fri Oct 12, 2012 9:12 pm
by gandalfbmg
First layer of Foam Coat is on.
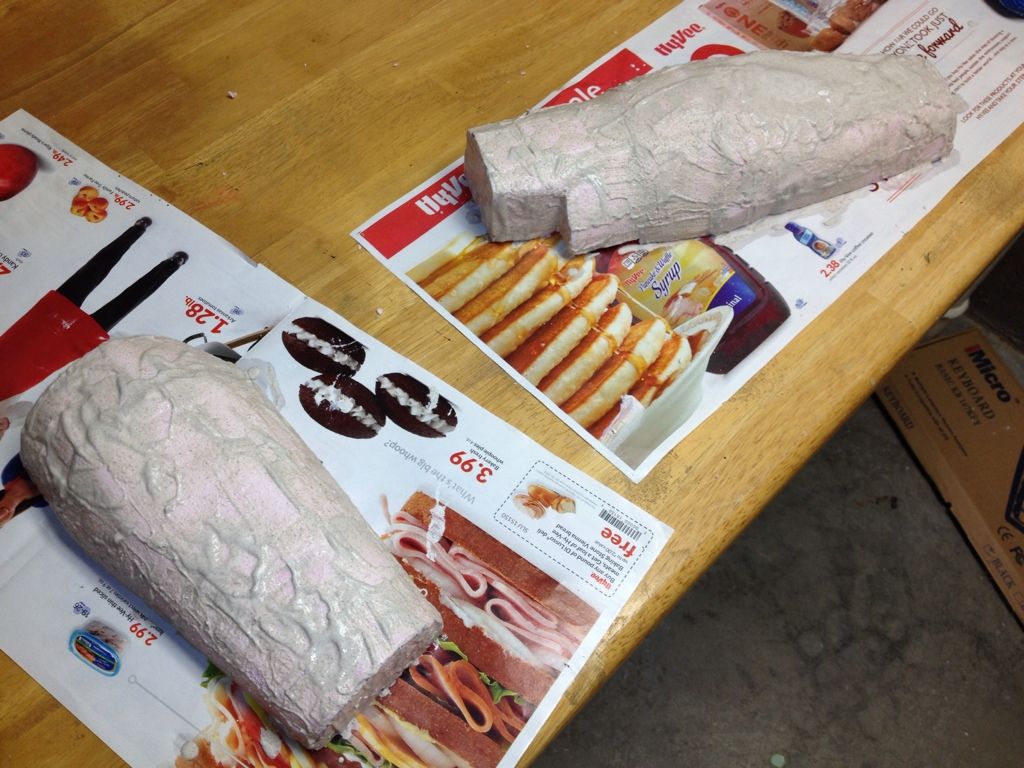
Re: Clone Wars style gauntlets
Posted: Mon Oct 22, 2012 8:24 pm
by gandalfbmg
So Zazarus took these to work and went to work on them with the belt sander to try and smooth them out a bit. The stuff proved a little too stonelike, so after a while we decided to do a coat or two of bondo over it and sand it and work it smooth that way, then do a really thin coat of the foam coat after that (now that I've figured out the trick is to getting it on thin and smooth is lots of water

). Though, I didn't have as much bondo as I thought and ran out about 2/3 of the way, and had to improvise with spot putty. So that's it until I can get to the store.
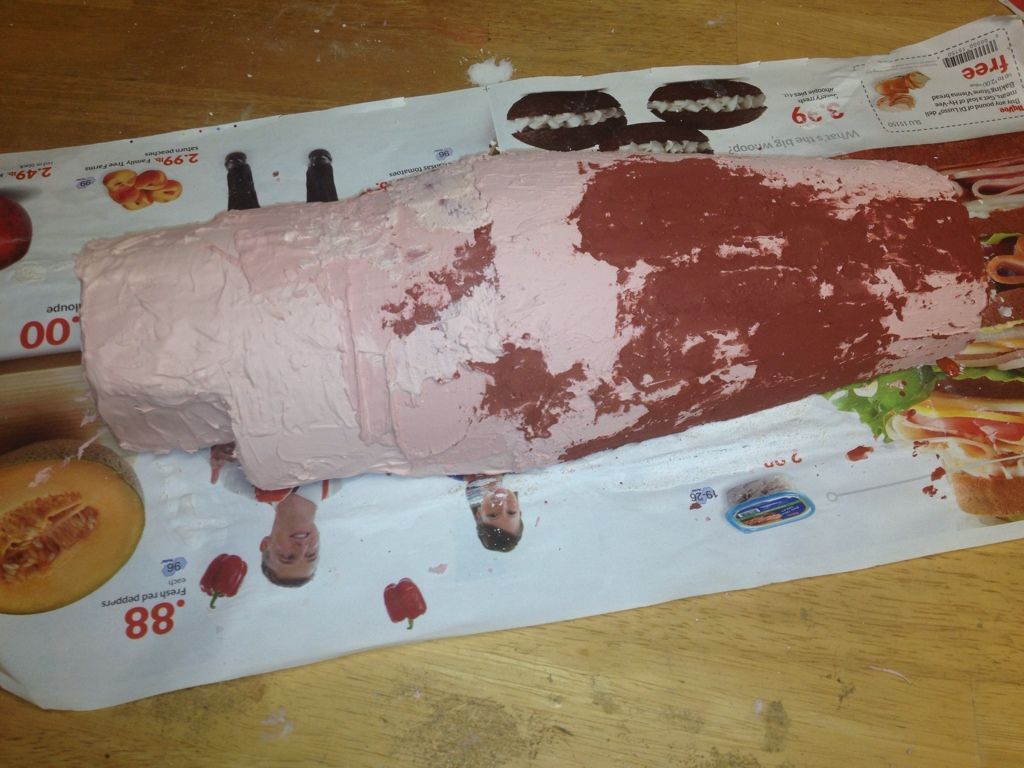
Re: Clone Wars style gauntlets
Posted: Sat Oct 27, 2012 9:16 pm
by gandalfbmg
Well, today was the vac forming class at Hammerspace workshop, so I took the pieces for a test run. They just had out thin plastic, but I figured it was good for a test run.
One I had pretty much finished (a top layer of foam coat over the bondo I'd been using to fill in the pits), the other just a layer of bondo and glazing putty, but about ready for a final foam coat.
lessons learned? W/o the foam coat, the bondo cracks and not-quite dried putty melts
But, I did a quick trim and taped them together:
This one is WAY too big for me and needs to be trimmed down. I feel like I'm getting close on the masters now.
Re: Clone Wars style gauntlets
Posted: Mon Oct 29, 2012 8:16 pm
by Culvan
Looks good. Harbor Freight's November coupon list will have a 15% off anything in the store coupon. Additionally their vacuum pumps are marked down right now too, so I'm probably going to buy a real vacuum pump. I'm not sure when I'll get around to hooking it up to my machine since it's not on my project list right now.
I'm such a slacker. I did convert a Pepakura file so I could import it into a CAD program. Because Pep is meant for paper the converted file is hollow. It would be useful if we could figure out how to make a solid object out of it. Certainly there are some possibilities here, but unfortunately I'm not all that skilled at applying them. Do we know anyone skilled at CAD manipulation who could do the next processing step?
Andy
Re: Clone Wars style gauntlets
Posted: Mon Oct 29, 2012 8:39 pm
by gandalfbmg
Doesn't steph Scheffner know cad?
Re: Clone Wars style gauntlets
Posted: Tue Oct 30, 2012 7:45 am
by gandalfbmg
Dave thinks she's probably out of practice. I'll have to keep thinking on that...
Re: Clone Wars style gauntlets
Posted: Tue Oct 30, 2012 1:54 pm
by timbremer
if you want to get one supper smooth then get some NSP sulfur free clay and put then coating of this on your positive and then use your finders or molding clay beginners tools you can get from walmart and smooth it out. i would recommend smoothon casting silicone, the nsp clay will not react with the silicon mold making mix. once the silicon has hardened up in a few minutes used plaster bandages you get through them as well and then order in ultracal 30 from some place like monster makers, say 50 pound bag(ultra cal 30 takes heat much better, that is what i use for cooking foam latex in my oven) then pour the ultra cal into the silicone mold just make sure the mold and plaster bandages are supported as much as you can on all sides so the ultracal doesn't distort it. once the ultracal sets up then remove it and you should have a good casting you can work with for a mold, if there are any imperfections just mix up some more ultracal and fill them in. check out the RPF as well, some of those guys will give their two cents as well...